Dry Mortar Mixing Station
The dry mortar plant is primarily used for producing wall materials, such as dry mortar, tile adhesive, wall putty, and ready-mix plaster. This complete production line features full computer control, high automation, a unique design, and a compact structure, ensuring simple operation, energy efficiency, and environmental friendliness. We offer simple dry mortar plants with production capacities ranging from 5 to 20 tons per hour, available in fully automatic or semi-automatic control systems. The number of cement storage silos is also adjustable to suit your project needs.
1.This machine is developed based on the essence of the technology and new generations owith new models. It has automatic feeding, pneumatic discharge, Bucket wall no accumulating block, no dead corner.
2.Fast mixing, only 8 minutes per mix
3.Small area, reasonable structure, simple operation, high production efficiency, no dust, power make up reasonale.
4.Reasonable configuration; Annual output about 20000-30000 tons of dry powder mortar production line, Usually need 4-6 material tank, two of large tanks for loading bulk cement and fly ash, the rest small tanks for Put light calcium, heavy calcium, sand, small materials and so on.
5.Bulk cement and fly ash into the tank do not need lifting equipment, Enter by the pump truck. The clever material distribution system supports a bucket elevator distribution job, thereby avoiding waste of resources.
6.The measuring system with the cooperation of the metering screw, import the raw materials into the metering warehouse,date feedback by sensors to realize raw material measuring. The metered material is guided into the main bucket lifter by screw conveyor and lifted to the upper part of the mixer to be mixed.
7.The transfer bin is a pneumatically open door, the material to be mixed can be quickly put into a gravityless mixer to achieve continuous production of dry mortar
Main details
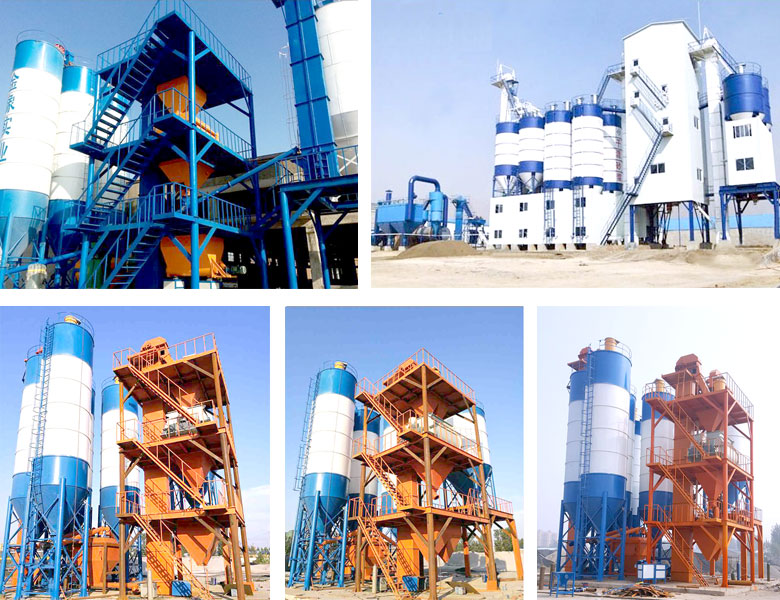
In terms of batching, the equipment abandons the traditional surface batching model and adopts the top dispensing mode of the tower layout, which greatly reduces the material proportioning and delivery time, improves the production efficiency, and reduces the material cost.
The mixing system uses 4cube large-capacity two-axis high-efficiency gravityless mixer with short mixing time, high mixing accuracy, and mixing rate of 3-5 minutes. At the same time of efficient production ensure the practical effect of the finished mortar is flawless.
Based on the common automatic packaging machine, the equipment is also equipped with an efficient bulk loading machine. This system can automatically carry out bulk operations on tank cars of 4 meters or less in size, meeting the requirements of bulk mortar in construction sites.
Full set of equipment is controlled by PLC automatic control system. The degree of automation management has reached the domestic advanced level.
Product advantages
1.This machine is developed based on the essence of the technology and new generations owith new models. It has automatic feeding, pneumatic discharge, Bucket wall no accumulating block, no dead corner.
2.Fast mixing, only 8 minutes per mix
3.Small area, reasonable structure, simple operation, high production efficiency, no dust, power make up reasonale.
4.Reasonable configuration; Annual output about 20000-30000 tons of dry powder mortar production line, Usually need 4-6 material tank, two of large tanks for loading bulk cement and fly ash, the rest small tanks for Put light calcium, heavy calcium, sand, small materials and so on.
5.Bulk cement and fly ash into the tank do not need lifting equipment, Enter by the pump truck. The clever material distribution system supports a bucket elevator distribution job, thereby avoiding waste of resources.
6.The measuring system with the cooperation of the metering screw, import the raw materials into the metering warehouse,date feedback by sensors to realize raw material measuring. The metered material is guided into the main bucket lifter by screw conveyor and lifted to the upper part of the mixer to be mixed.
7.The transfer bin is a pneumatically open door, the material to be mixed can be quickly put into a gravityless mixer to achieve continuous production of dry mortar.
The quality of their products significantly improved our project
timelines. Exceptional support throughout the process!
Why Our Dry Mortar Plant?
✅ Fully Automated Production
PLC + Touchscreen Control System (Recipe storage: 50+ formulas)
±0.5% Batching Accuracy (Cement, sand, additives)
✅ Zero-Waste Design
Dust-Free closed-loop system with pulse bag dust collector
3-layer sand drying & screening (optional thermal oil/rotary dryer)
✅ Modular & Compact
Tower-Type (for fixed large-scale) / Horizontal (for mobile projects)
Containerized design for easy shipping & installation
✅ Wide Material Adaptability
Handles sand (0-5mm), cement, fly ash, redispersible polymer powder (RDP), fibers
Technical Specifications for Dry Mortar Mixing Plant
Model | Annual Output(T/300day/24h) | Total Power | Theoretical yield(t/h) | Full volume(m³) |
wz-1c | 50 thousand | 11KW | 5 | 2 |
wz-2c | 100 thousand | 18.5KW | 10 | 2 |
wz-4c | 200 thousand | 22KW | 20 | 4 |